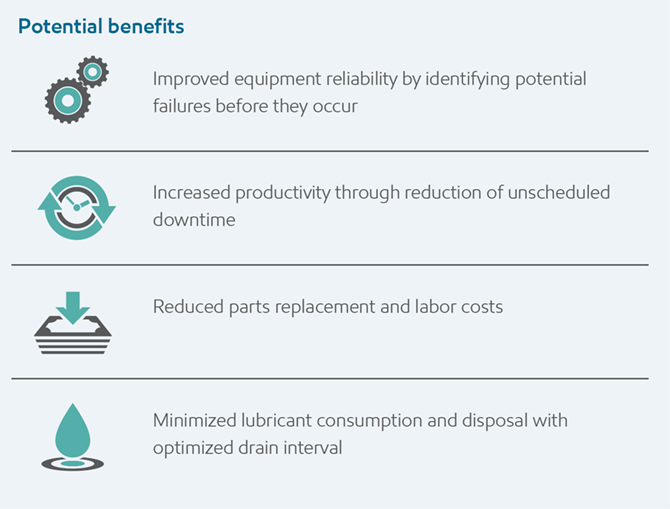
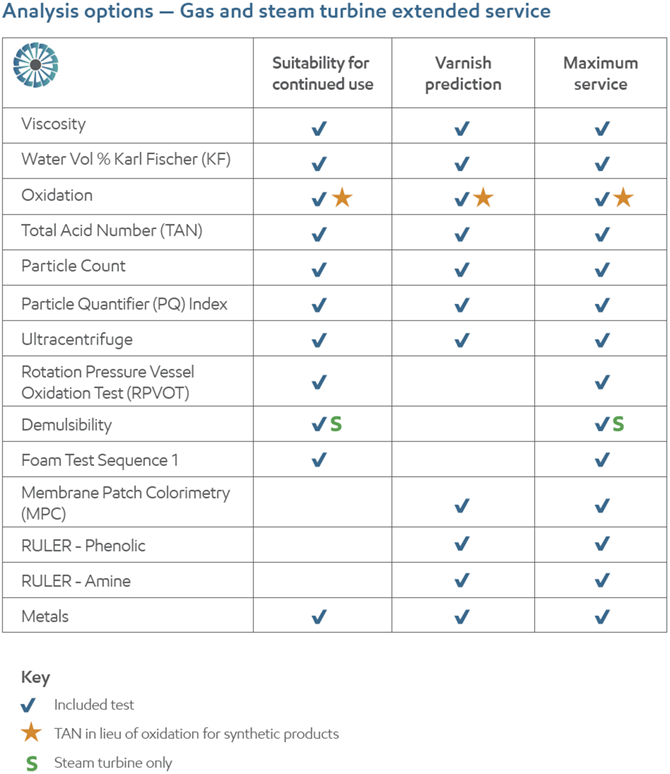
Test | Purpose | Importance of test |
---|---|---|
Total Acid Number (TAN) | To measure acidic oil oxidation byproducts | An elevated Total Acid Number may indicate increased oil acidity resulting from increased oil oxidation. |
Demulsibility | To measure the ability of an oil to separate water | Steam turbines often expose the turbine oil to water from condensed steam. The ability of the oil to shed water will have a direct impact on its long-term oxidative stability and equipment rust |
Foam Sequence I | To measure the potential of an oil to build and maintain foam | Foam can lead to operational issues like improper oil level indication or reservoir overflow |
Membrane Patch Colorimetry (MPC) | To measure color change of a filter patch due to varnish vs. clean patch as energy change (ΔE) | Color and light blockage from lubricant deposits on a membrane patch can indicate the presence of varnish in the oil |
Metals | To determine the presence and levels of metallic content in the oil, including contaminants and wear particles | The level of wear metals helps determine if equipment components are wearing or if harmful contamination has entered the oil. The level of metals that are part of the additive chemistry is also reported |
Particle Count Analysis | To measure the level of particulate contaminants in the oil |
|
Particle Qualification (PQ) Index | To determine ferrous metal fatigue failures and metal-to-metal contact not usually detectable with some spectrographic analysis |
PQ Index can detect at an early stage:
|
Oxidation | To determine the level of lubricant oxidation and deterioration |
Oxidation can mean:
|
Remaining Useful Life Evaluation Routine (RULER) - (Linear Sweep Voltametry) | To measure individual antioxidant concentration in oil compared to a new oil reference (%) | Understanding antioxidant reserve in turbine oils can be helpful in predicting end of oil life and may provide insight on varnish formation |
Rotating Pressure Vessel Oxidation Test (RPVOT) | To measure the remaining oxidation stability of an oil | Oxidation stability is a key performance feature in turbine oils. As an oil oxidizes, the equipment is more prone to build varnish |
Ultracentrifuge Rating (UC) | To measure varnish deposit formation in oil | Elevated deposit formation can signify increased potential for varnish formation |
Viscosity | To determine the oil’s resistance to flow |
|
Water | To detect presence of water contamination | Water contamination may cause severe corrosion and subsequent wear, poor oil film thickness or hydrogen embrittlement |