Preventing hydraulic oil contamination | Mobil™
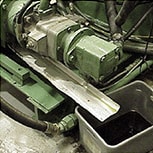
If converting hydraulic oil within a system, operators must be mindful of cross- contamination. Hydraulic oil contamination can have an adverse effect on its performance capabilities, and in great enough quantity (typically more than five percent), contamination can adversely affect the biodegradability and toxicity of the fluid. However, by completing a flushing procedure in the system prior to filling with hydraulic oil, operators can help mitigate potential performance issues that can be caused by the mixture of the fluid and other contaminants.
Operators should note that in newly installed systems, it may be necessary to remove an internal coating of rust preventives, resulting from preservative fluids that run through the system prior to shipping. These protective coatings on components, such as pumps and valves, should be cleaned off of componentry prior to filling the system with new hydraulic oil, as they can act as contaminants in the hydraulic oil.
To convert a system to new hydraulic fluid, complete a flush and fill procedure:
- If necessary, drain as much oil as possible from the cylinders, filters, pumps and valves. Wipe the reservoir and other accessible interior spaces with clean, lint-free rags. In newly installed equipment, look carefully for pipe scale, weld spatter, shavings and other debris resulting from installation and remove any solid contaminants from the system.
- Replace filters if necessary.
- Charge the system with sufficient hydraulic fluid to ensure circulation to all components.
- Operate the system at normal temperatures and loads for at least one hour after reaching these temperatures. Monitor differential pressure drop across the filter. A filter change may be necessary during this flush because contaminants in the system are incompatible with the hydraulic fluid. If this is the case, change the filters and continue to operate the system at normal temperatures, but at reduced loads, until the hour of flushing is complete and the filters are clean.
- Drain the hydraulic fluid, while hot, and clean any contaminants from the system. Replace filters.
- Fill the system with hydraulic fluid and begin operation.
- Posted
- 22-02-2016