Basics of an oil analysis program | Mobil™
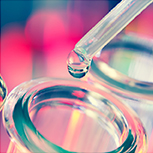
Oliver Boissel, Products Technology – EAME Industrial Products Technical Advisor, ExxonMobil Fuels & Lubricants
The goal of a proactive oil analysis program is to track gradual changes in fluid properties, contaminants and machinery component wear debris so that corrective action can be initiated in a controlled, planned and timely manner. It’s easy to see the importance of a proactive oil analysis program, so here’s a six-step process to get you off and running:
- Identify mission-critical equipment
It’s not always necessary to perform oil analysis on every single lubricated system in your plant. Identify critical applications that would seriously jeopardize production if they were to shut down unexpectedly. - Register your equipment
It’s important to have your equipment properly registered with the lab. This will support routine trending and play a key role in early detection of lubricant or equipment problems. There’s no need to decide which tests are appropriate; the lab has already established application-specific test slates. - Establish oil analysis best practices
Establish a consistent how-to process for taking oil samples from your equipment, and train your maintenance personnel to use this practice. Proper sampling techniques are essential to the value received from oil analysis data. - Oil sample and analyze
Retrieve samples and send them to the lab as soon as possible, as samples that are set aside may deteriorate and give a non-representative result. Thorough oil sample analysis results help determine your oil and system condition. - Interpret
Review the results and determine what, if any, action is required. If your results show an alert status, this does not necessarily mean imminent failure. Seek consultation on any alert result and, if possible, resample the equipment lubricant to confirm status before taking corrective actions. - Take corrective action and document results
Document all corrective actions taken as a result of oil analysis. Historical oil analysis and corrective action documentation are helpful when contacting an OEM for warranty work.
- Posted
- 22-02-2016